Common Questions and Their Answers About Our Industry
- Matthew Briggs
- 4 days ago
- 4 min read
Navigating the landscape of our industry can often feel overwhelming, especially for those who are new to it. This blog post aims to clarify some of the most common questions we receive. By providing detailed answers, our goal is to help individuals and businesses make informed decisions.
Common Questions
One of the most frequently asked questions in our industry revolves around the types of services we offer. We often encounter potential clients who are unsure about which services are best suited for their needs. Understanding the wide range of offerings is essential for making the right choice.
For example, if you are looking for custom manufacturing solutions, it's important to consider whether you need prototyping, production runs, or perhaps even post-production services. Knowing the distinctions can save you time, money, and resources.

Another common misconception is that all manufacturers are the same. In reality, companies often have different specializations, certifications, and capabilities. When you choose a manufacturer, consider their expertise in your specific field. For instance, some focus on automotive parts, while others may specialize in consumer electronics or textile manufacturing.
What Are the Main Benefits of Our Services?
When contemplating our services, many people ask about the advantages they can gain. Here are a few specific benefits:
Cost Efficiency: Leveraging our expertise can lead to significant savings. We bring industry knowledge to identify cost-effective solutions without compromising quality.
Quality Assurance: We adhere to strict quality control measures that ensure the highest standards in production. This includes regular audits and incorporating advanced technologies during the manufacturing process.
Scalability: As your business grows, our services can easily scale to meet increased demand. Whether you need small batch productions or large-scale manufacturing, we have the resources to accommodate your needs.

Customization: We recognize that every client is unique. Our processes allow for tailored solutions that meet individual specifications, helping you stand out in the marketplace.
By understanding these benefits, potential clients can more effectively evaluate the value of our services.
What Does the FAQ Refer To?
One often overlooked aspect is our dedicated faqs section. This resource provides additional insights into common inquiries and concerns. It addresses various topics, from technical specifications to order timelines. Whether you have questions about materials, processes, or shipping methods, our FAQ section is designed to clarify fundamental points.
Consider checking the FAQ for information on typical lead times. Knowing how long it usually takes to process orders can help manage expectations and improve communication between us and our clients. Additionally, if you’re unsure about product minimums, our FAQ can provide clear guidelines.

How Do We Ensure Quality in Our Process?
Quality assurance is a cornerstone of our operations. Many clients are curious about how we maintain such high standards. Here are several methods we employ:
Standardized Procedures: Each phase of the manufacturing process is governed by standardized operating procedures. This ensures consistency across all projects.
Regular Inspections: We conduct regular inspections throughout the production process. This helps identify potential issues early and reduces the likelihood of defects in final products.
Employee Training: Continuous training programs for our employees ensure that everyone is up-to-date with the latest techniques and technologies. This leads to better performance and higher quality output overall.
By asking about our quality assurance measures, potential clients can gauge how seriously we take our commitment to excellence.
How Can Businesses Maximize Their Benefits from Our Services?
When businesses collaborate with us, there are several proactive measures they can take to maximize their benefits:
Clear Communication: Setting clear goals and expectations upfront can streamline processes and lead to more satisfactory outcomes.
Detailed Specs: Providing thorough specifications for projects enables more accurate quotes and reduces back-and-forth. This saves time and improves efficiency.
Ongoing Collaboration: Establishing a collaborative relationship allows for feedback that can lead to continuous improvement. Frequent check-ins can help address questions before they become bigger issues.
Regular Updates: Keeping us informed about any changes in your production needs or business direction helps us adapt quickly and meet changing demands.
By implementing these strategies, businesses can achieve better outcomes and develop a more fruitful partnership with us.
What Should You Consider When Choosing a Manufacturer?
Selecting the right manufacturing partner is crucial for any business. Here are a few practical tips to consider:
Experience: Assess how long the company has been operating and whether it has experience in your industry. Established companies often have proven track records and extensive knowledge.
Certifications: Investigate whether the manufacturer has obtained relevant certifications. These can serve as indicators of quality assurance and compliance with industry standards.
Client Reviews: Researching testimonials and case studies can provide insights into the manufacturer’s reliability, customer service, and product outcomes.
By weighing these factors, you can make a more informed decision about which manufacturing partner is most suitable for your needs.
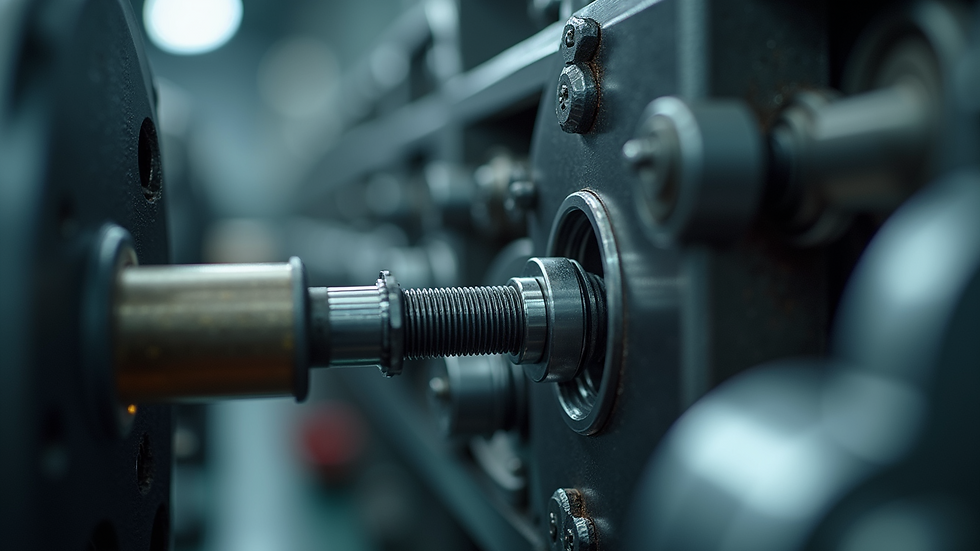
Understanding these common questions and their answers about our industry can empower clients and businesses. By being informed, you can make better decisions that ultimately lead to greater success. Feel free to reach out with any additional questions or visit our faqs for more detailed information.
Comentarios